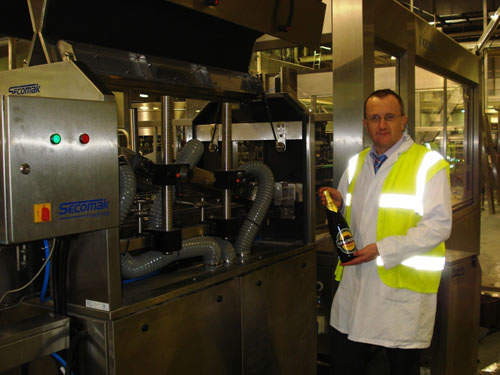
Paul O’Sullivan, responsable de l’assurance qualité de Magners, montrant une pinte Magners nouvellement embouteillée.
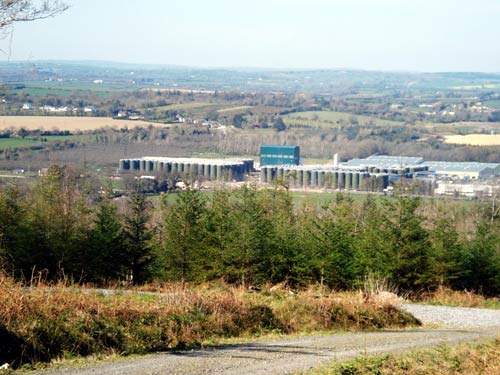
L’installation de Clonmel.
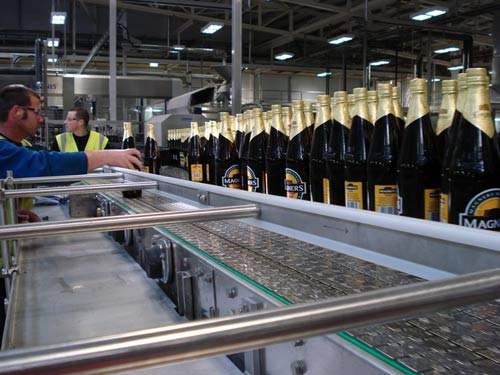
Les bouteilles doivent être sèches pour que l’étiquetage soit précis et pour éviter les problèmes de suremballage du film.
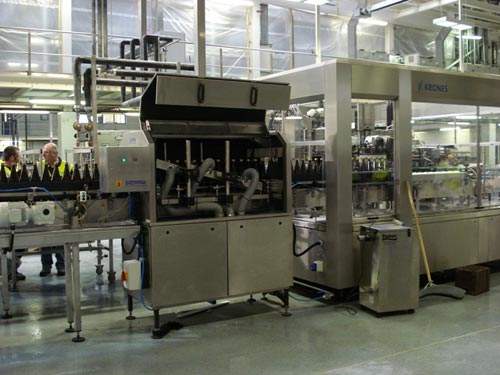
La ligne de remplissage et le séchoir.
Magners Irish Cider est maintenant l’une des marques de cidre les plus connues et les plus vendues sur le marché britannique. Magners est en fait la marque numéro un de cidre emballé au Royaume-Uni et est maintenant disponible sur 17 marchés à travers le monde.
Grâce à une campagne publicitaire télévisée réussie de 20 millions de £ en cours depuis 2006, l’image ternie du cidre en tant que boisson populaire a été modifiée et il a de nouveau été introduit sur le marché populaire. Les ventes ont augmenté de plus de 40% depuis 2006, mais se sont rapidement refroidies en 2008 en raison des conditions du marché, de l’augmentation des coûts et du mauvais temps.
Le cidre a été conçu pour être servi sur de la glace (ce qui a suscité des marques similaires sur glace telles que Bulmers Original) et a reçu une image à la mode attrayante pour plaire à la population d’âge du marché de 20 à 30 ans.
La boisson, fabriquée par Bulmers Ltd en Irlande, est disponible en canettes de 500 ml, en bouteilles d’une pinte et en formats de bouteilles à col long de 330 ml dans tous les grands supermarchés britanniques. Le cidre a également fait forte impression sur le marché du cidre à la pression dans les maisons publiques britanniques après être devenu disponible pour la première fois en mai 2008.
Les marques Bulmers et Magners appartiennent à C & C Group, qui est un groupe de boissons responsable de grandes marques telles que Carolan Irish Cream, Tullamore Dew (whisky), Frangelico (liqueur de noisette), Ritz (perry) et Irish Mist (whisky).
Lignes d’embouteillage
En mai 2007, l’usine de fabrication de Magners à Clonmel dans le comté de Tipperary a vu ses lignes d’embouteillage améliorées avec trois nouveaux systèmes de séchage de bouteilles Secomak Powerstrip. Cela était nécessaire en raison d’un taux de rejet plus élevé que la normale en raison d’étiquettes mal alignées sur la pinte et les bouteilles à col long de 330 ml produites à l’usine (augmentation du gaspillage et des coûts). Pour les Magners, l’aspect et la présentation du produit sont tout aussi importants que le produit à l’intérieur de chaque bouteille. Magners a des exigences très strictes pour la composante d’étiquetage du processus de production.
Le cidre est mis en bouteille à froid (en utilisant la technologie de remplissage à froid Krones), ce qui provoque la formation de condensation sur le goulot et le corps des bouteilles en verre. Les gouttelettes d’humidité doivent être éliminées avant le processus d’étiquetage ou les étiquettes peuvent glisser lorsqu’elles sont appliquées et se désaligner. En outre, l’eau recueillie sous l’enveloppe de papier d’aluminium sur le goulot de la bouteille causant des problèmes d’hygiène.
Par conséquent, les séchoirs à bouteilles Powerstrip étaient situés juste avant l’entrée des bouteilles dans les étiqueteuses à grande vitesse. Ceux-ci ont été conçus de manière à pouvoir assurer un séchage sans traces à une vitesse de ligne de bouteilles de 68 000 bouteilles par heure.
Paul O’Sullivan, responsable de l’assurance qualité de Magners, a déclaré: « Les séchoirs à bouteilles Secomak ont eu un effet immédiat sur la qualité. Ils nous permettent d’atteindre des vitesses d’embouteillage et d’étiquetage très élevées en toute confiance. Ils donnent également à nos clients la tranquillité d’esprit supplémentaire que les cols des bouteilles sont secs sous l’emballage en aluminium. »
Solution de séchage Powerstrip
Le système Powerstrip est une solution de séchage entièrement modulaire qui peut permettre de combiner une gamme de modules de séchage pour presque tous les processus de production à base de convoyeur.
Le système utilise une gamme de technologies qui peuvent inclure des couteaux à air entraînés par soufflante, des composants de vide et d’aspiration induits, des micro-buses d’air comprimé et des systèmes de contrôle de pointe. Les systèmes sont configurés sur mesure en utilisant les technologies les plus appropriées en fonction de l’application.
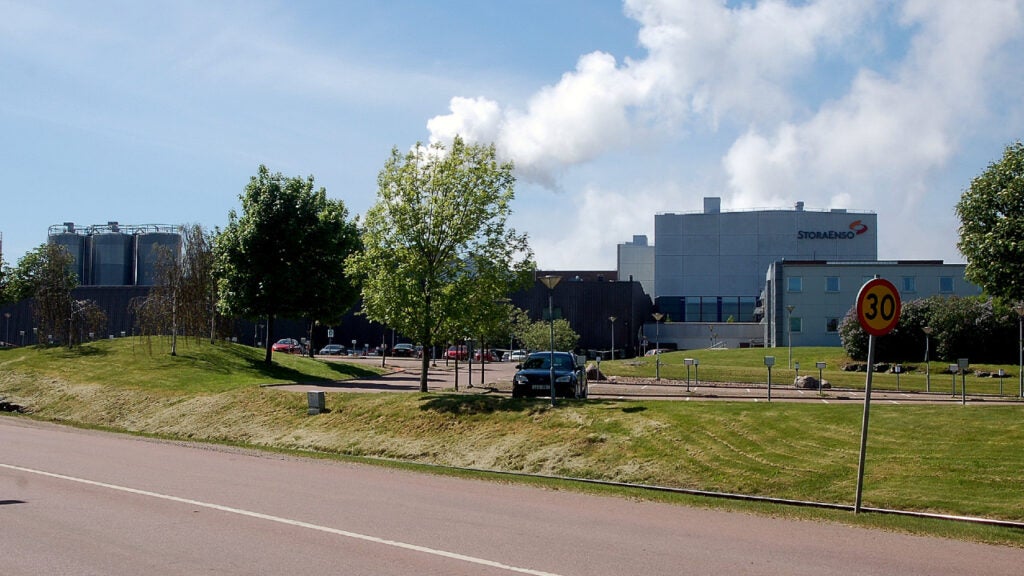
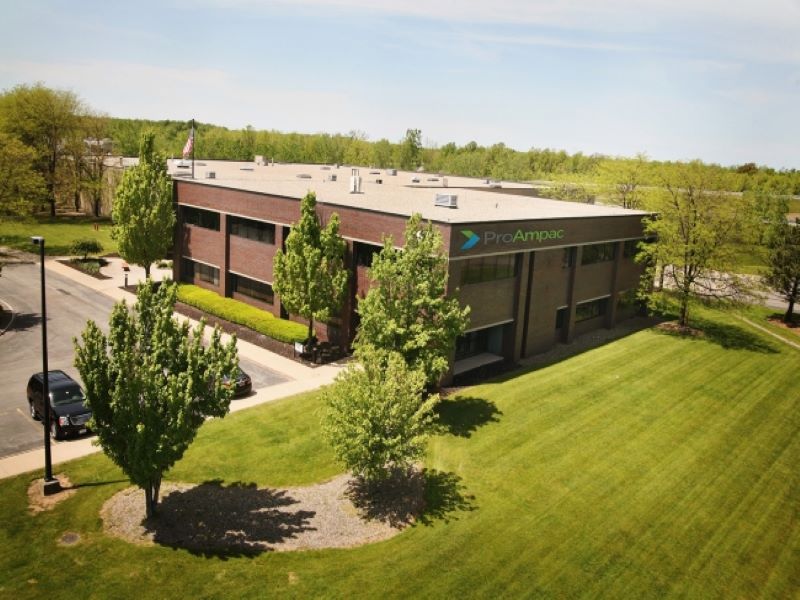
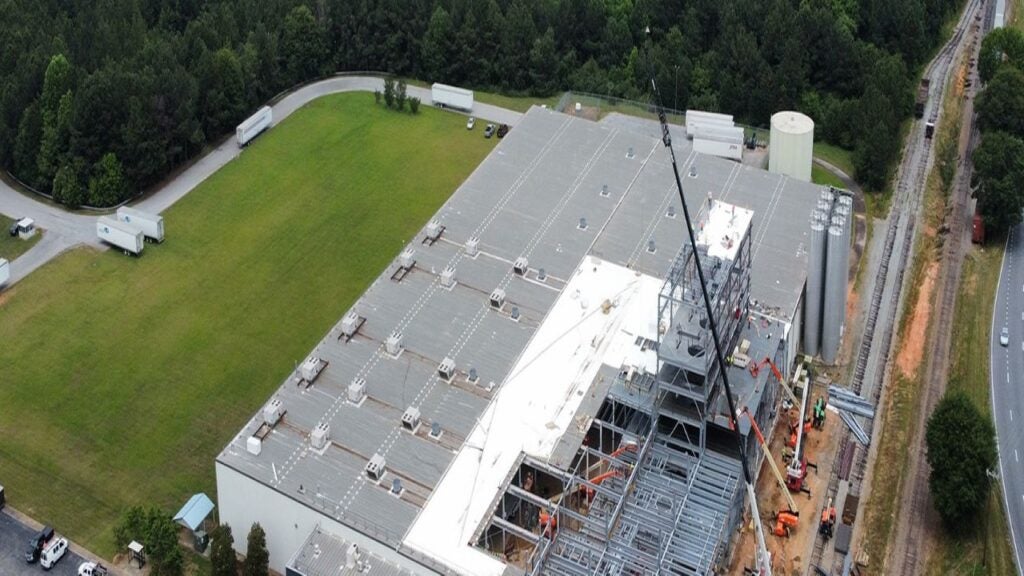